Classification of Warping Machines
- textilecoach
- Feb 8, 2021
- 3 min read
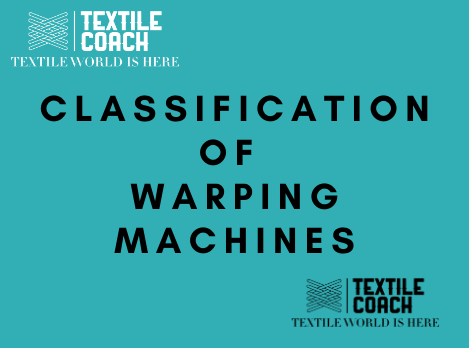
Warping: it is defined as a process of combining of ends from cone or cheese or spool or double flanged bobbin on to warper beam.
Every warper beam is provided with gedgion pin, riuffle and flanges. Every beam is characterized by a specific width. The width may be adjustable or standard.
Classification of warping machines:
Direct warping: beam warping or drum driven warping, spindle driven warping
Indirect warping: sectional warping
Beam warping/Drum driven warping:
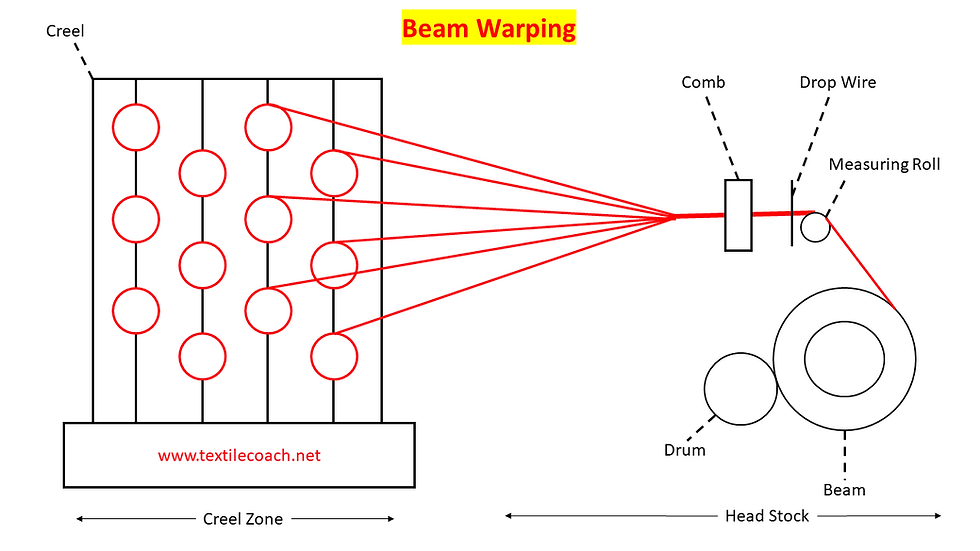
It is used for long warp system yarn of all types.
It is used to prepare single color, multi colored warping and used to prepare the warp of single ply yarn and multi plies.
First of all warp is wound on to the warpers beam then the warp yarn from these warpers beam transferred on the weavers beam during sizing.
It is used with creels with maximum capacity of 1000-1500.
The beam is driven with frictional contact with the drum.
It is most popular method in organized sector.
Stainless steel drum with internal expanding brake used.
Heavy, sturdy, rugged with 1 inch thickness is used.
The warp yarns from the creels passes through the tensioner guides and then enters into reed and wound on to the warpers beam.
Spindle driven:
This method is only useful for filaments as chaffing of filaments is prevented due to friction contact.
Here the beam is mounted on the spindle.
Sectional warping:
This system is preferred to produce stripe patterns, warping of multi plies yarn, multi colour warp and continuous filament yarns. This method is more useful when required warp length is low. A pattern is nothing but arrangement of colored threads. For example a pattern consists of 23 white, 18 red, 23 white, 18 blue, 23 white, 18 green. It indicates that white is constant and all other are constant but basically their pattern is irregular.
A regular pattern is the one where the threads are same. Sectional warping is preferred for short length of warps and is more preferable in handloom sector. It is called indirect warping because warping is done first then beaming takes place.
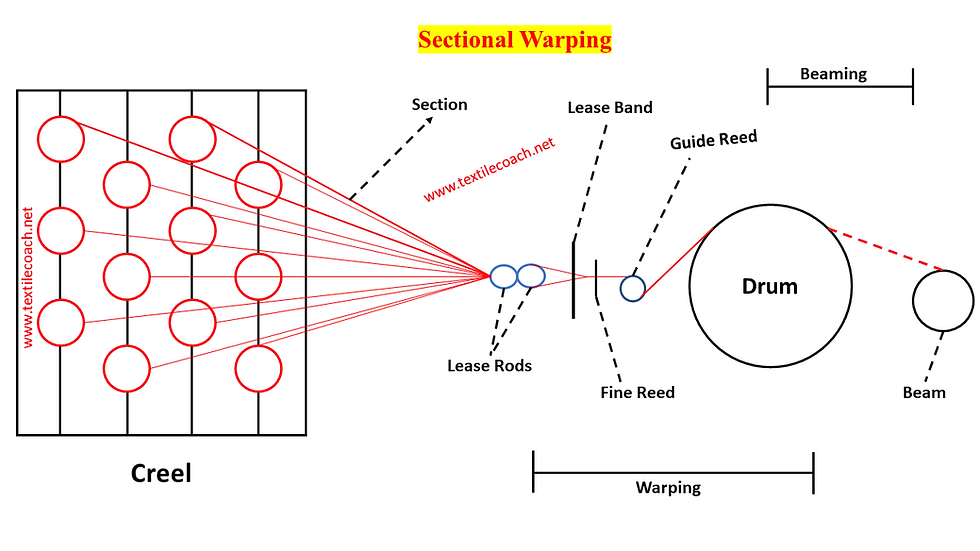
Figure shows the passage of material. Creel consists of thread guide, tensioner, package holder etc. creel capacities may be 100 to 400. The total number of ends collected in the form of a section from the creel is passed through lease rods whose function is to separate the layers of the section into two. The warp is then pass through lease rods which is shown in fig 1.1 dents with block.

Some of ends are passed through block and some are passed through free dent to separate warp again into 2 layers for insertion of lease bands. The warp then passes through fine reed, on to the guide roll and finally on to the drum in the form of a section. This section is wound with a set length at certain speed. When the set length is complete, the traverse head is moved and the next section is started. All sections are wound for same set length side by side.
When required number of sections are completed, the warping process is completed. The drive to drum is disconnected and the beaming process starts.
The yarn is rewound from the drum on to the beam. Speeds of warping and speeds of beams are separate. The beam used in weavers beam with beam ruffle and beam flange as shown in figure 1.2.
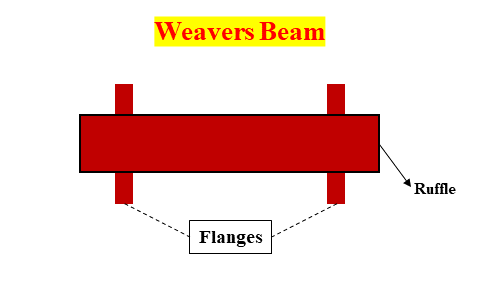
Ball warping:
This process does not produce a beam as it is an intermediate process for storage, transportation and dyeing of yarn.
The main object of this process is to prepare a log for the rope of a dyeing machine. Magazine creels are used for creeling of yarns in the form of cheese.
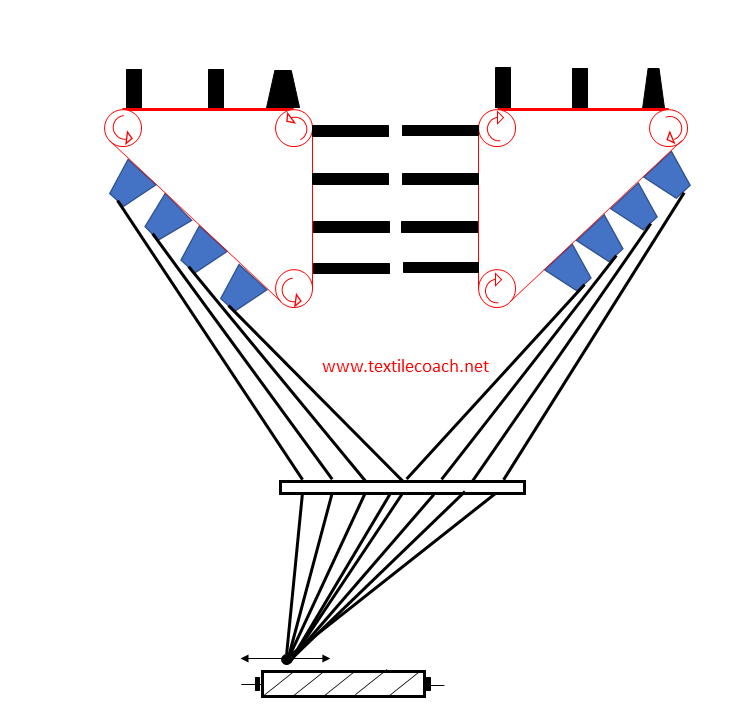
Passage of material:
It involves creeling of multiple ends of yarn and collecting them into an untwisted rope for dyeing.
In this process, 350 to 500 ends are pulled from the creel. Then the yarn transfers through a reed, which keeps each warp yarn separate and parallel to its neighboring ends.
For every 1000 or 2000 yards of yarn, a lease string is placed to separate warp yarns.
Then the yarns passes through the trumpet where condensing of yarn takes place into rope form.
Then the rope is wound on to a long cylinder called a log on a machine called as a ball warper.
Then the dyeing in rope form takes place.
Once the dyeing is done, then the rope form of yarn converts into sheet form by transferring yarn into tensioning devices. This process is called re-beaming or long chain beaming which is done before sizing.
Comments