Moisture relation of textile fibers
- textilecoach
- Nov 22, 2020
- 4 min read
Updated: Jan 8, 2021
Humidity:
It is defined as the amount of moisture present in the atmosphere. It can be described in terms of Absolute humidity (AH) or Relative Humidity.
Absolute Humidity (AH):
It is defined as the amount (weight) of water present in the unit volume of moist air, it was the actual density of water vapor present in the atmosphere which is expressed in-terms of grains per cubic foot (gr/foot³) or grams per cubic meter(g/cm³).
Relative Humidity (RH):
It is defined as the ratio of actual vapor pressure to the saturated vapor pressure at the same temperature, expressed in terms of percentage.

Moisture Content (M) (MC):
It is defined as the ratio of weight of water to the total weight of material, which is expressed in percentage.
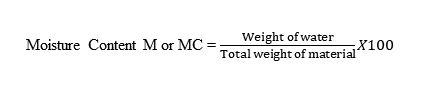
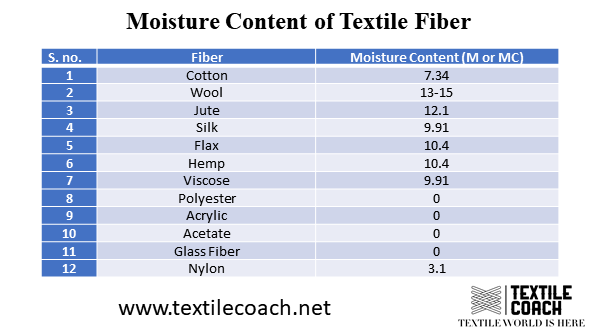
Moisture Regain (R or MR):
It is defined as the ratio of Weight of water present in the material to the Oven dry weight of the material, which is expressed in percentage.


Influence of Moisture on Fiber Properties:
Under natural conditions there will be constant change in the moisture present in the air, which results in the change of amount of moisture in the fiber. As a result, change in the physical properties of the fiber such as Dimensions, Tensile strength, Elastic Recovery, Elastic resistance, Rigidity etc.…
1. Cotton absorbs more amount of moisture when it is exposed to high humidity air, which results in the increase of strength and weight of the fiber.
2. In case of wool fiber with increase of moisture in air strength decreases.
3. In case of man-made fibers like viscose, Acetate etc. strength decreases, and elongation increases with increase of moisture in the air.
4. In case of synthetic fibers like Nylon, Terylene there will ne no effect as these fibers are not fully hydroscopic.
Influence of Moisture on Processing:
Textile processing is influenced by the change of amount of moisture in the atmosphere. Under ideal humidification conditions following are the advantages takes place in textile processing.
1. Static charges generation can be reduced.
2. Pliability will increase so that materials are made easier workable.
3. Allows for the retention of moisture already present in the material.
4. Permits grater bodily comfort for the workers.
Standard atmosphere:
It is defined as an atmosphere at the prevailing barometric pressure with a relative humidity of 65% and a temperature of 20oc (68oF).
Standard testing atmosphere:
It is an atmosphere with a relative humidity of 65±2% and a temperature of 20o±2oC (68o±4oF).
In the case of tropical regions like India, temperature of 20oC is difficult to obtain and so a higher standard temperature of 27o±2oC (81o±4oF) is used.
Factors affecting the fiber regain:
1. Relative Humidity:
Regain of the fibers increases rapidly at low humidity followed by an almost linear portion and then a more rapid rate at high humidity’s.
2. Time:
A material placed in a given atmosphere takes a certain amount of time to reach equilibrium. The time of conditioning depends on several factors such as size and form of the sample, the material, external conditions etc...
3. Temperature:
Regain decreases as the temperature increases.
4. Previous history of the sample:
Previous history of the sample like wet or dry will affect the equilibrium regain. The hysteresis effect is the perfect example, in the wet processing, when oils, waxes, and all other impurities are removed the regain may change. The application of tension will also change the regain.
Effects of regain on fiber properties:
1. Dimensions: Absorption of moisture is accompanied by changes in the dimensions of fibers. Swelling takes place mostly in the transverse direction. since the water molecules penetrate between the parallel molecular chains and exert their forces outwards. The length of the fiber increases slightly due to absorption of moisture. But the net result of absorbed moisture in fabrics is a decrease in length i.e., shrinkage, and a function of the fiber assembly structure. Dimensional change in the fabric as it passes from one atmosphere to another may result in the wrinkled appearance of suits tailored in one atmosphere and worn in others, especially in climates where high humidity’s are found. Advantage of swelling is taken in the design of water proofs, A close weave can be used for water proof fabrics which becomes even closer as the component yarns swell, thus preventing the penetration of water. 2. Mechanical Properties The general effect of water molecules in the fiber is to reduce the strength of the fiber. But in the case of vegetable fibers such as cotton and flax strength is increased Also the stress strain curve assumes a different form and the yield point may be shifted. Extensibility, crease recovery flexibility and ability to be set by finishing processes are the other mechanical properties affected by regain. 3. Electrical properties The electrical resistance of fibers varies with different regain values. When the sample is dry. practically the resistance for the flow of electrical current will be maximum and when it is wet, it will be minimum. The dielectric characteristics and the susceptibility to troubles are also affected by the amount of moisture in the material In processes where the regain of the product is required to be reasonably constant, as in warp sizing and cloth finishing both the resistance and the dielectric effects are utilized in the design of control systems. 4. Thermal effects When moisture is absorbed by textile materials, heat is generated. This heat is termed as the heat of absorption. Suppose a sample of dry weight is 1 gram, and it is completely wet. The heat evolved is termed as heat of wetting and it is expressed in calories per gram of dry material.
Comentarios